Rock salt is the Iowa DOT’s primary deicing material to combat winter storms. Each year, the department uses approximately 200,000 tons of rock salt to keep Iowa highways clear of snow and ice.
Typically, the rock salt used in Iowa comes from underground mines in Kansas or Louisiana. The salt is purchased each season through a competitive bidding process for delivery directly to 113 delivery points managed by the Iowa DOT.
Kansas salt is shipped to Iowa delivery points using rail and trucking. The Louisiana salt is brought to Iowa via barges on the Mississippi River and then trucked to the delivery point.
The Iowa DOT also has an active testing program for new deicing materials or additives. The goal of that testing program is to find an alternate deicing product or additive that works as well or better than rock salt with minimal impact to the budget, environment and infrastructure.
Brine Information
This brine information is not an endorsement of any particular brand or product, but simply an account of the Iowa DOT's experiences as it moved from not using salt brine to using more than 12 million gallons in a time span of 10 years.
List items for Brine Information
Brine is defined as any liquid saturated or nearly full of chloride.
This could mean that any dry chemical, freeze-point depressant containing chlorides, such as magnesium chloride, sodium chloride, potassium chloride or calcium chloride when mixed with a liquid would be considered a brine.
For the purposes of this discussion, the information provided will concentrate on a brine made from the mixture of sodium chloride (rock salt) and water. This is the brine most often used in Iowa for prewetting and anti-icing operations.
Brine has been used in many countries for years as both a prewetting agent for dry materials and as an anti-icing agent for the proactive treatment of snow and ice.
Antiicing is placing the brine on the roadway surface before a precipitation event. This action helps prevent the snow and ice from bonding to the pavement and makes the snow easier to plow off.
Prewetting is the practice of wetting salt granules with brine, before being spread on the pavement. Prewetting helps salt from bouncing off the road during application and as vehicles drive by. It also provides a bit of moisture to help the salt crystal dissolve, which is necessary for ice-melting action.
A study conducted by the Michigan DOT measured the amount of chemicals left on the roadway after a dry (no brine) spinner application of materials and found that nearly 30 percent of the materials left the roadway after application and landed on shoulders or in ditches due to bouncing, leaving only 70% of the total applied material on the roadway to do productive work.
Similar studies conducted in Switzerland and Germany measured the amount of dry chemicals that remained on the roadway after vehicle movement and found that after five vehicles had passed, only 30 percent of the dry materials remained on the roadway. After 100 vehicles had passed, only 20 percent of the dry chemicals remained to do the job. When the materials were prewet with brine and after five vehicles had passed, 93 percent of the materials remained on the road; and after 100 vehicles, 80 percent remained on the roadway surface. If a dry mix is being used to remove snow and ice, it is obvious that a roadway with large volumes of traffic will quickly lose most of the materials onto the shoulder or ditch where it is of little help to melt snow and ice. Brine is a very effective tool to make the best use of our winter chemicals.
The use of salt brine for prewetting and anti-icing is no longer experimental or unusual. All of the Iowa DOT's snowplow trucks are equipped with units that prewet dry materials at the spinner. Anti-icing equipment is available statewide to anti-ice when conditions make it an effective strategy.
Many cities and counties, including many of the major metro areas, are now active users of salt brine.
- Rock salt can be spread more uniformly and less is wasted on shoulders and ditches reducing the impact to the environment.
- Materials adhere to the surface because the salt and brine mixture has a thicker consistency. The slurry-like mixture tends to "plop" onto the roadway and better stay where it lands.
- Melting begins faster because a liquid has been introduced to the salt. (Salt must find moisture before it can begin to work.)
- Spreading speeds can be increased because more material stays on the roadway.
- Because brine begins working and diluting as it hits the surface, it will dry much more rapidly, returning the roadway to normal winter driving conditions much sooner.
- Residual salt may remain on the road that will immediately begin working with the next storm.
- When dry materials are prewet with brine, application rate can actually be cut back 20 percent to 30 percent because more of the material remains on the roadway. The additional brine adds some quick melting action.
- Can be used as a deicer on very thin layers of frost or black ice, but with caution. Salt brine is not recommended for snowpack unless it is treated regularly and frequently with a sufficient quantity of salt brine and/or salt brine and rock salt. Brine alone will rapidly dilute and if an insufficient concentration is maintained, may refreeze before it can burrow through the snow or ice pack.
- Application prior to a storm can help prevent snow and ice from bonding to the pavement.
- Helps keep roadway wet longer into a storm or in the case of a very light precipitation event, possibly throughout the storm.
- Makes cleanup quicker and returns roads to normal driving conditions more rapidly.
- Reduces labor hours.
- Reduces wear on ice blades and underbody plows.
Making brine is a fairly simple process requiring only two ingredients — water and salt. However, it is very important to ensure the brine is made to the ideal concentration of 23.3 percent of salt, by weight. This is the highest concentration of salt that will stay in solution without settling out, and is the concentration with the lowest freeze point. Brines that are mixed with not enough salt don’t have as much ability to melt and are susceptible to dilution and early re-freezing. The phase diagrams help explain how the freezing point (eutectic temperature) of common deicing chemicals will change when mixed at different concentrations.
Hydrometer Used to Measure Salt Solution
A hydrometer or salimeter is needed to measure the brine concentration. Hydrometers can be purchased with readouts in specific gravity, percent solution or salt concentration.
Iowa DOT Brine Makers
In 1995, the Iowa DOT purchased its first commercially produced brine maker after years of experimentation with homemade units. Today, all DOT maintenance garages have brine making capability and thousands of gallons of brine storage on-site. Brine making speed and volumes are dependent primarily on the water supply. With 1-inch water lines, brine making will be a much slower process than when a 2-inch supply line is available.
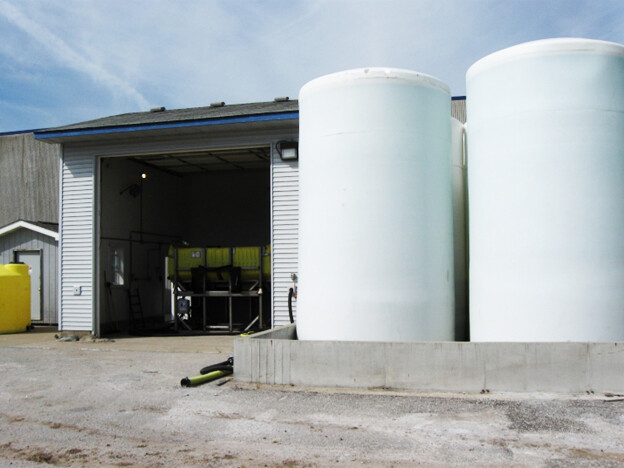
If you are considering adding a brine-making production plant to your facility, there are a few other lessons learned in the Iowa DOT's experience that you may want to be aware of or consider.
Water
- Water supply line size can limit production capabilities. A minimum of a 2-inch supply line is recommended if substantial quantities of brine will be produced.
- Consider a separate water meter for the brine maker to avoid paying sewer charges on the water used to make brine.
- Facilities with well water must carefully consider if the additional load required to make substantial quantities of brine can be "borne" by the natural water supply.
Salt
- Despite what you may think, very fine salt does not work well in brine makers. A standard gradation salt with as few impurities as possible is best.
- If salt is too fine, the water can not circulate freely through the salt and you may end up with a lump of salt that will not appropriately go into solution.
- If impurities are allowed to build up in the mixing tank, it is more difficult to get a consistent, fully concentrated salt solution and production may suffer.
Facilities
When selecting a brine-production facility, consider the corrosive nature of the salt and minimize those effects wherever possible.
- Consider a separate building or section off a portion of a building so corrosiveness can be controlled or contained. Separate heating and ventilation systems are recommended.
- Electrical connections and equipment are especially subject to corrosion. Investigate weatherproof switches, fans, etc., and consider mounting as much equipment as possible outside the building.
- Use moisture-resistant lighting and encase all interior wiring in well-sealed plastic conduit for protection.
- A standard overhead door will have a shortened life span due to the corrosive atmosphere. Consider the additional replacement expense down the road or investigate upgrades that may better withstand the corrosion.
Storage
- Consider the need and/or local or state requirements for secondary containment.
- Make sure tanks used outdoors contain a UV inhibitor.
- A gallon of salt brine is more than 2 pounds heavier than a gallon of water. Make sure the tanks you purchase are designed to handle the additional weight.
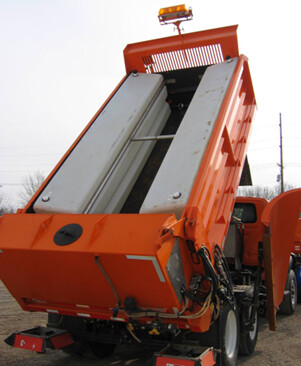
900-Gallon wedge tanks fit inside the dump truck box, and granular salt can be loaded in the space between. A tank tailgate is also fitted.
The Iowa DOT has used a variety of brine application equipment, dependent on the particular needs of a location. Though there are many variations, the following photos demonstrate some of the prewetting and anti-icing equipment that has been successfully used by the Iowa DOT.
A wide variety of different types of nozzles and spray bars have been used in the Iowa DOT's history with anti-icing. Some of the first units used were simple gravity fed units, where the size and number of holes drilled in the piping regulated the application rate. The current units are controlled by a ground speed controller for precise, consistent application rate
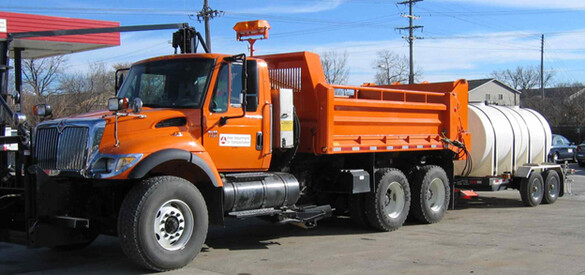
A truck with a 2,500-gallon trailer.
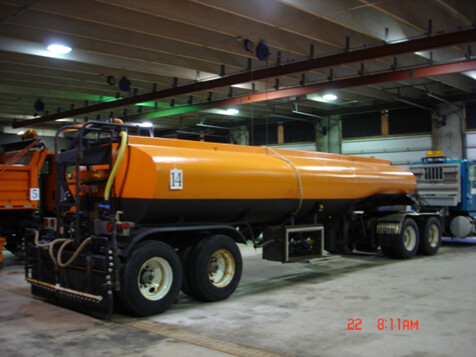
A 5,000-gallon tanker.