On this page...
The Iowa DOT, a national leader in accelerated bridge construction (ABC), accomplished another “first.” The U.S. 6 bridge over Keg Creek in Pottawattamie County was completely prefabricated off-site. The road was closed for just two weeks to replace the bridge. Normally, using traditional construction methods, the road would have been partially or fully closed for several months, causing major traffic delays.
Back to topProject Information
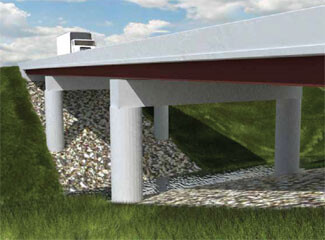
In early 2010, Iowa DOT was asked by the Transportation Research Board (TRB) Strategic Highway Research Program 2 (SHRP2) to participate in a demonstration project involving accelerated bridge construction (ABC). The scope of the SHRP2 project R04, Innovative Designs for Rapid Renewal, was to develop standardized ABC systems for nationwide use. The Iowa DOT, a national leader in ultra-high performance concrete (UHPC) bridge applications, partnered with the consulting group HNTB Corp. who led a four-year national study on ABC for the SHRP2. HNTB and Iowa State University, along with other industry partners, developed standards and specifications to be used for future ABC projects across the country.
As part of the study, the Iowa DOT provided a bridge replacement site to demonstrate the viability of one of the ABC concepts developed. A bridge on U.S. 6 over Keg Creek was chosen as a test site, a three-span 210’ x 47’ steel/precast modular structure with precast bridge approaches. Under this ABC concept, the U.S. 6 bridge was constructed with minimal impact on traffic, the road being closed for only two weeks. With traditional construction methods, this project on U.S. 6 would normally have required the partial or complete closure of the road for several months, resulting in substantial traffic disruption.
The bid price for the Pottawattamie County demonstration bridge project, including additional grading and drainage improvements, was $2.6 million, which is approximately 30 percent more than a similar three-span conventional bridge. To help cover the additional cost of using the new technology, the Iowa DOT received a $400,000 (or up to 20 percent of the total project cost) Highways for Life (HfL) grant and another $250,000 from the SHRP2 program.
One of the project’s goals was to choose a bridge replacement project that would be innovative and repeatable. A three-span bridge was chosen because that particular configuration is common throughout Iowa and other states. Bridge engineers wanted to ensure that what was learned from this project would be applicable to other bridges in the future.
Ahmad Abu-Hawash, previously Chief Structural Engineer for the Bridges and Structures Bureau, said that in addition to the prefabricated nature of the entire structure, several other elements of this project stand out. He said, “Typically, when we use precast deck panels in bridge construction we specify a concrete overlay to protect the joints between panels. This overlay could add weeks to the construction duration, therefore, it became obvious that a more durable joint is needed in lieu of the overlay. Given Iowa’s past experience with UHPC, the design team recommended UHPC be used in the joints. The primary advantages of this joint material are low permeability and high strength meaning an impenetrable and stronger joint.”
Another design element that differed from some conventional bridge construction was the use of preassembled rolled steel girder units. Abu-Hawash said, “The superstructure used in this bridge consisted of rolled steel beams with concrete deck modules prefabricated off-site. The exterior modules also included traffic railing. I believe this is the first time rolled steel girder/concrete deck modules were assembled off-site and jointed on-site with UHPC.”
Because this was a demonstration project, a webcam was used to document construction. Abu-Hawash explained, “As we have done on other innovative projects, construction site Web cameras document project activities and provide uninterrupted access to any interested parties via the Internet. In cooperation with Iowa DOT, the National Academy of Sciences plans on producing a documentary video with national distribution to promote the innovations being demonstrated on this project.”
Aside from the webcams, Abu-Hawash and others involved in the project presented the findings at a construction workshop for other state DOTs, FHWA and other interested parties.
Abu-Hawash sees future uses for complete precast bridge replacements. “With our aging infrastructure and damage from natural disasters such as floods, states sometimes need a way to replace bridges quickly. The experience gained from this project will give us the knowledge to utilize these technologies when needed and where appropriate.
The U.S. 6 bridge project was one of 15 awarded grants in the 2010, $20 million round of HfL funding. The HfL program seeks to get states, engineers and contractors to adopt proven innovations and technologies leading to:
- Improved safety during and after construction.
- Reduced congestion caused by construction.
- Better quality of the highway infrastructure.
These funds are to be used for incentives to state DOTs to demonstrate innovative technologies and practices that can be used to build projects more safely and quickly, result in longer-lasting highways, and achieve a higher level of user satisfaction. Information from these projects is shared with the whole transportation community to accelerate changes that will improve the safety and performance of our highways, and reduce the impact of construction and maintenance on highway users. These projects also have performance goals as a part of their HfL application.
Back to top